Noticia - Asesorías / Consultorías / Legal
La generación de vapor y el tratamiento de agua para las calderas – eficiencia energética con la franquicia SoftEnergía
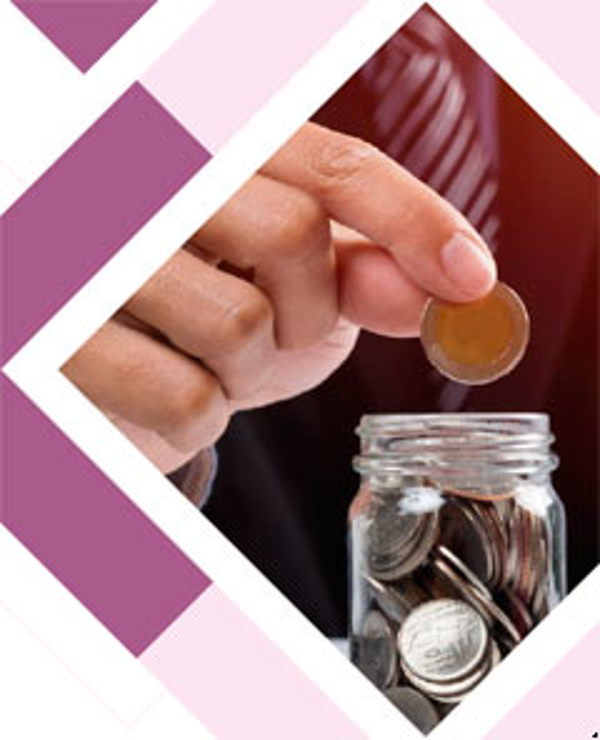
La utilización del agua a nivel industrial tiene un fin mucho más complejo que su uso para el consumo diario como un elemento potable. Técnicamente se utiliza para transferir calor en los procesos de calentamiento. De esta manera se puede suministrar energía calorífica considerando la eficiencia energética y sirviendo para la generación de vapor a través del uso de calderas de distintos tipos. El agua es uno de los recursos más valiosos para producir electricidad. Es por ello, que su implementación en los procesos previos a la producción de energía debe realizarse con sumo cuidado para que todo el proceso en las centrales pueda funcionar y se realice con eficiencia energética.
Al tratar el agua correctamente en las calderas, se pueden evitar problemas de corrosión, arrastre de condensado, formación de incrustaciones, entre otros. Estos factores son contraproducentes para la pureza y calidad del agua. Asimismo, tratar el agua de forma apropiada permite una vida más útil del sistema de generación y distribución del vapor, mantener una eficiencia térmica adecuada, reducir los costos por mantenimiento y trabajar con eficiencia energética. Existen algunos requerimientos para el tratamiento del agua de alimentación y para el agua interna de las calderas de baja y alta presión para prevenir los problemas ya mencionados. Los tratamientos externos y los internos son esenciales para garantizar que el agua sea tratada cabalmente.
Pruebas químicas para las calderas de alta presión
El tratamiento para las calderas varía acorde a las condiciones que presenten y si es posible de acuerdo a la eficiencia energética de la planta. No obstante, todas requieren de un control periódico para mantener las condiciones de las mismas. Las pruebas químicas que se realizan a las calderas de alta presión dependen de la relación del agua de aportación al condensado para producir el agua de alimentación de la caldera. Algunas de las pruebas que deben realizarse son las siguientes:
· Prueba de acidez o alcalinidad: se utiliza para controlar la corrosión y la incrustación.
· Prueba de dureza, calcio y magnesio: tanto el calcio como el magnesio pueden utilizarse para determinar la cantidad de cal y sosa que se le necesita agregar al agua de caldera para controlar las incrustaciones que produce la dureza.
· Prueba del hidróxido: se determina para controlar la corrosión, fragilidad, arrastre e indirectamente el control de la incrustación. Sin calderas que trabajen con un nivel de eficiencia energética apropiado, el proceso para generar energía no será el adecuado.
· Prueba del fosfato: se controla para producir incrustaciones solubles que puedan purgarse fuera de la caldera para que funcionen con una eficiencia energética apropiada.
· Prueba del sulfito: se realiza para evitar la corrosión a través de la concentración de este combinado con la concentración del oxígeno disuelto en el agua.
· Prueba del hierro: se pone en práctica para observar si el retorno del condensado tiene exceso de óxido de hierro proveniente de las tuberías anexas a la maquinaria que trabajan con vapor y que funciona bajo una eficiencia energética apropiada.
· Prueba del cobre: tiene un efecto similar a la prueba del hierro pero la fuente suele ser los equipos de bombeo con piezas de cobre.
· Prueba de conductividad eléctrica: por medio de esta prueba se determina la cantidad de sólidos que se encuentran en el agua y se usa para controlar la purga.
Solubilidad e incrustaciones en las calderas
Dos de los principales problemas que se presentan en las calderas y que las hace trabajar con menor eficiencia energética son la solubilidad y las incrustaciones. La primera varía de acuerdo a la temperatura de la solución, donde el efecto inmediato es producir una sustancia insoluble. Las sustancias que se hacen más solubles con el incremento de temperatura tienen una relación de solubilidad positiva pero cuando sucede lo contrario tienen una relación negativa. El grado de solubilidad es importante para determinar cuándo una determinada concentración de impurezas en estado disuelto puede precipitar como sólidos externos a la solución.
Las incrustaciones son depósitos adheridos sobre la superficie de transferencia térmica en el lado de agua de las calderas producidas por impurezas sedimentadas como el sulfato, el carbonato, el hidróxido, el nitrato cálcico, el fosfato, entre otros. Cada uno de estos elementos disminuye la eficiencia energética de las plantas donde se encuentran las calderas.
La incrustación puede provocar algunos cambios químicos en el agua de la caldera. Uno de ellos es como factor aislante del calor, lo que hace que las calderas pierdan rendimiento y eficiencia energética. Otro, es la provocación de temperaturas peligrosamente altas debido a que es un mal conductor del calor. Además de esto, provoca la evaporación del agua haciendo que los depósitos sean cada vez mayores donde los gases son más elevados.
Para identificar las incrustaciones es necesario realizar una revisión periódica de las calderas, ya que estas se presentan en forma de costras que pueden adherirse fuertemente a la superficie de las calderas. Otras producen depósitos blandos y son más sencillas de desprender pero todo depende del elemento con el cual se hayan formado. Para prevenirlas es necesario tener en cuenta la utilización de agua dura en las calderas por la presencia de sales de calcio y magnesio. Por otra parte, se debe tener un límite de impurezas determinado para no sobrepasar cantidades que puedan contribuir con las incrustaciones. La purga es clave para controlarlas.
Para evitar las incrustaciones, el primer paso que se debe tener en cuenta es el tratamiento externo, el cual suele ser el tratamiento del agua, la reducción de sólidos en suspensión por filtrado, ablandamiento de la cal, equipo de intercambio de iones, desmineralizadores, eliminación de gases y oxígeno, entre otras. El tratamiento interno se basa en la selección de productos químicos para controlar las impurezas minerales especialmente cuando la presión de la caldera va creciendo. Por otro lado, se tiene el tratamiento combinado con fosfato que suele ser utilizado para calderas que trabajan por debajo de 600psi(42kg/cm2). Independientemente del tratado que se le realice a la caldera, lo más importante es evitar las incrustaciones y todo aquello que debilite la composición de los materiales de las mismas.